Warm Block
Brewhouse Equipment: Efficiency meets Quality
Brewhouse equipment plays a crucial role in achieving maximum efficiency, short brewing sequences, highest yields, and bright worts for commercial breweries and large-scale breweries. At Ziemann Holvrieka, we offer technologically sophisticated brewhouse equipment designed to meet the specific needs and requirements of our customers in the commercial brewing industry. Our warm block solutions are tailored for optimal performance and exceptional brewing results.
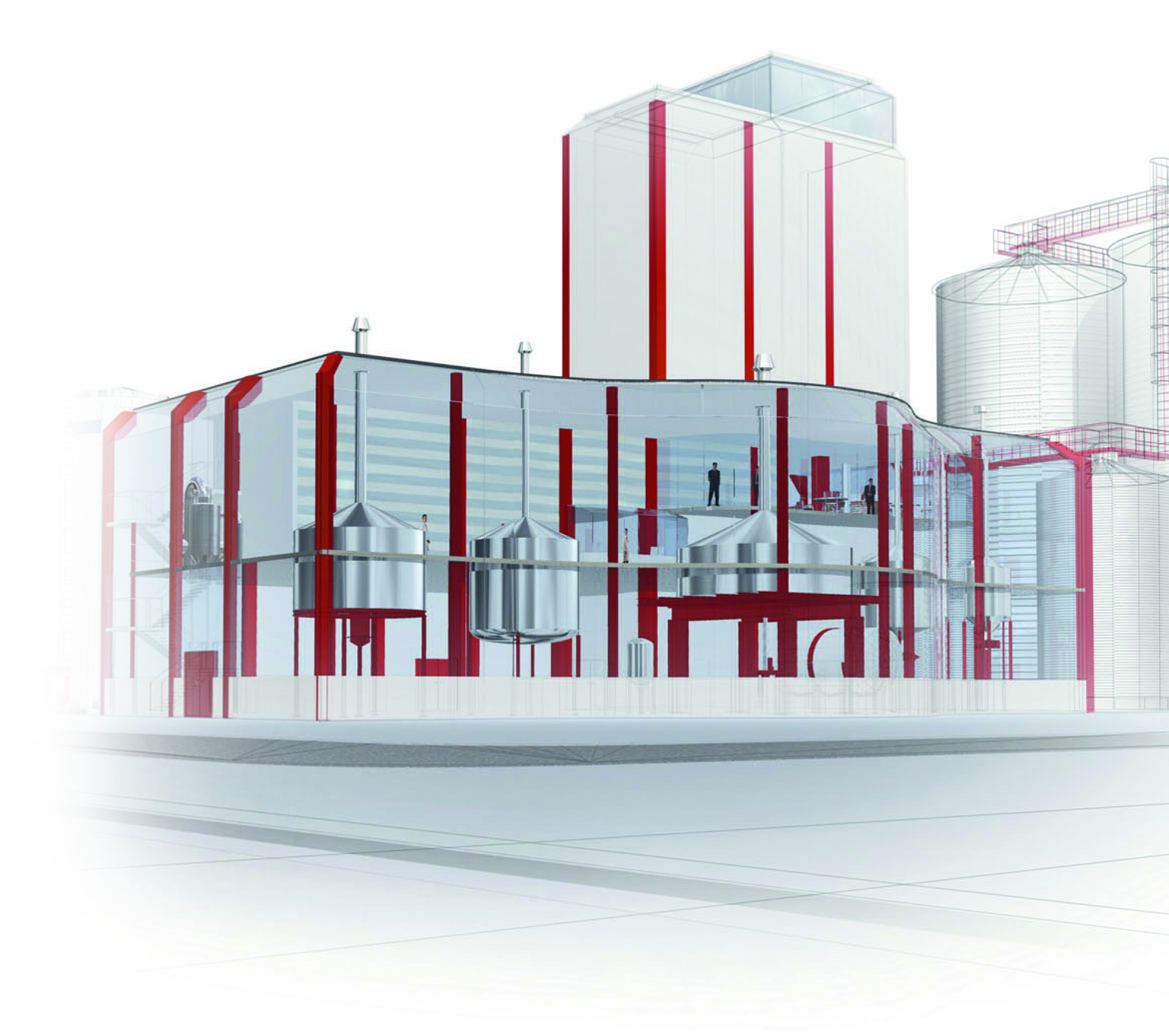